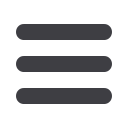
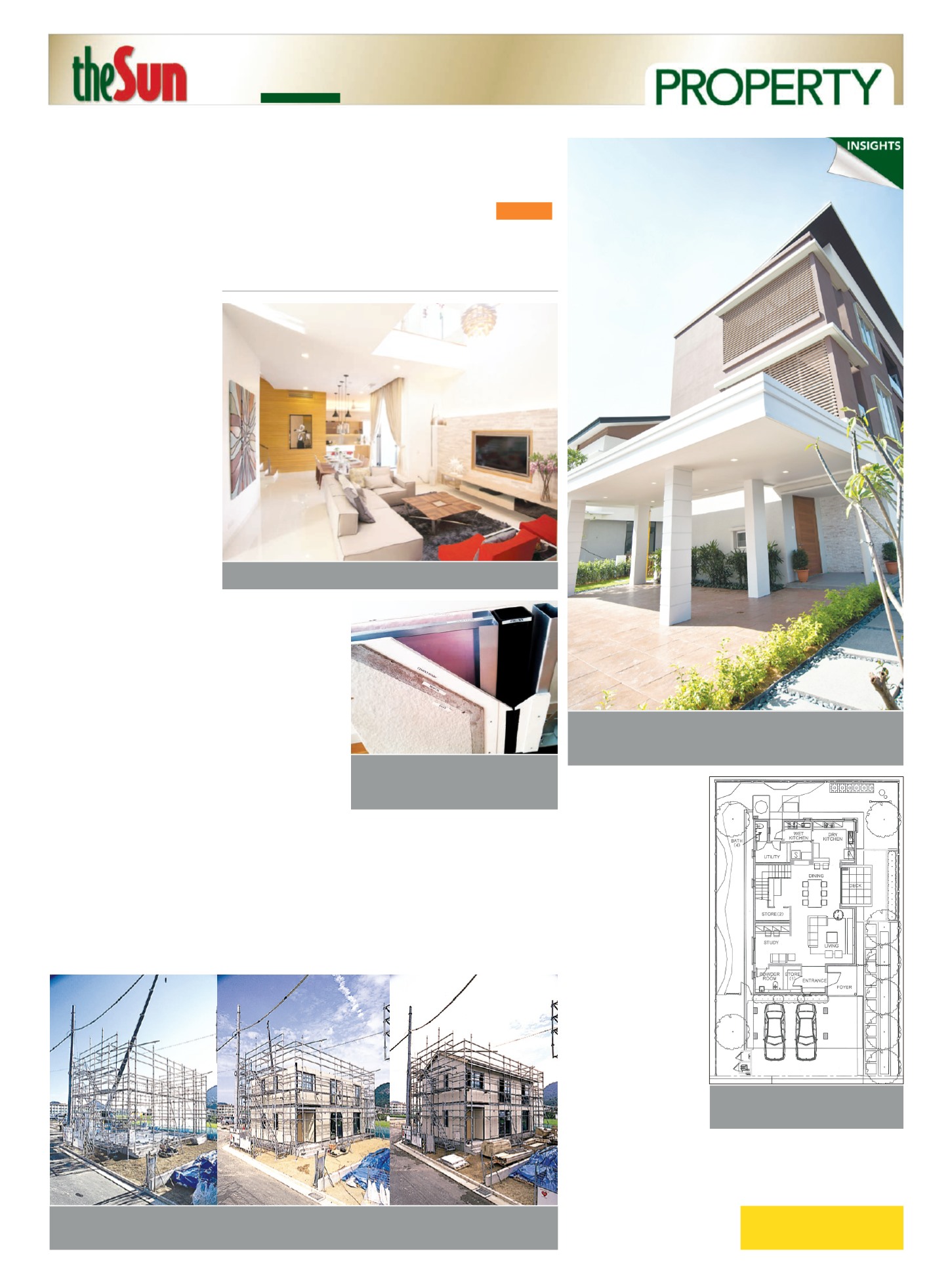
Email your feedback and
queries to:
[email protected]X
>The nation’s first prefabricatedprototype
housebyDaiwa
Prefabricated
housing
L
AST
week’s article explored
the basics and fundamentals
of what prefabricated houses
are all about. This week,
we provide deeper insights and
a clear, comprehensive picture of a
prefab house, complete with floor
plan, construction process and the
finished product.
QUICK DELIVERY
In this day and agewhere time is
money, speedy delivery of a house
would incite a celebration for
both the developer and house buyer.
For the developer it would lead to a
shorter timeframe for recovering his
or her investment and generating
profits. The buyer in turn, receives
the keys to their property faster.
Says Daiwa House chief architect
Kanta Tokuda: “In the case of Japan,
it takes about four months (to erect
a prefabricated house) from the
signing of the sales and purchase
agreement, to completion of a unit
(which in Japan is at the average size
of 2,200 sq ft).” The processes
involved include:
1) signing of SPA (sales and
purchase agreement);
2) beginning of prefabrication
at factory;
3) commencement of foundation
work and construction;
4) assembling and erectionwork;
5) wood and plumbingwork
plus interior fit-out;
6) testing after completion; and
7) hand over.
Economy of scale is a widely
cited benefit in the case of
prefabrication as components and
entire homes can be produced in
large quantities. With prefab, there
is also value in faster project
schedules, not tomention fewer
weather delays andmore efficient
use of materials. Optimisation and
quality control are prefab’s biggest
and best features. “Aprimary
benefit for the buyer is the
predictability, which actuallymeans
less defaults and defects after
the keys are handed over,” shares
Tokuda. He adds that the purchaser
not only receives the advantage of
getting his or her house fast but with
a degree of surety of the outcome.
BETTER QUALITY
With components and parts of the
home all manufactured under
uniformed control and precision
calculations by machines, there is
little room for defects. Where
Daiwa is concerned, Tokuda
assures that steel is used
as beams, columns and wall frames.
This provides sound stability.
“Many homes in Japan are
prefabricated. They can withstand
the Japanese typhoons and
earthquakes and are very secure.”
While the metal components are
structures are also created to stave
off water leakage and such.
SMART HOUSE AND GREEN
TECHNOLOGY
Every room in the prototype house
is designed with two windows that
allow natural air to flowwithin. All
windows are also fitted with
elegant-looking mosquito screens.
These allow them to be left open
without inviting unwanted insects
treated with anti-rust and
given an electrostatic
coating, wooden
materials are applied
with anti-termite
treatment prior to
installation. All
components are basically
“fitted in” or “screwed
on” using nuts and bolts.
Doors and door frames
are also created with
much thought put into
the design. People-
friendly and created
with safety, security
and innovative design
in mind, the doors
prevent fingers from
getting trapped.
The design of the
prefab prototype house by Daiwa
House inMalaysia is enhanced
with accessories, appliances and
fittings of premium quality. Tokuda
also makes it a point to inform that
the bathroom can be installed in
just a couple of days. He highlights
the high quality materials, cleverly
designed and purposefully
created fit-outs used in the modern
design lavatory. The plumbing
system applied in Daiwa’s prefab
PART2
into the home.
The prototype house is
also fittedwith a solar water
heater systemwith panels
placed on the roof. The
house is also equippedwith
unique features that help
reduce electricity usage.
Although all five bedrooms
are fittedwith air-
conditioners, Tokuda says
that electricity consumption
is low as the house “runs” on
a smart house technology
systemcalledHEMS (Home
EnergyManagement
System) that improves
overall efficiency, conserves
energy and saves costs, as
well as the environment.
“The systemenablesmore
effective energy
consumption, reduces
carbon dioxide emission and
promotes energy savings in
the home,” explains Tokuda.
Moreover, the exterior
walls of prefab houses in
Japan are insulated to
promote air circulation
functions (by filling the
interior of the wall with
thermal insulating material
and adding a dense outer
layer of insulating glass wool
board). There are also two coats
of waterproofing applied, a
primary coat to the wall’s exterior
and a secondary to the wall’s
interior. What this does is that it
allows moisture to escape through
the air permeating layers which
also inhibits the formation of
condensation. Walls of prototype
houses inMalaysia have been
modified to suit our climate.Quick,
clever and clean ... are we now
ready for prefab housing?
Daiwa House prefab houses in Japan comewith after-sales service and
a guarantee of up to 50 years. The above picture is of the exterior of the
prefab prototype house in Sunway Eastwood, Seri Kembangan.
Themodern-inspired living area in the prefab prototype house.
Cross section of themany layers of a “wall”,
modified to suit our climate – the column,
pillar, plaster board, insulation panel, steel
frame, cement board, mortar and paint.
ON FRIDAY
OCTOBER 10, 2014
1) Construction of ground floor
pillars and external walls.
2) Construction of first floor beams
and external walls.
3) Construction of roof truss and
roof panels.
Ground floor plan of theMalaysian
prefab prototype house.